TIG welding.Explanation of the high-quality fusion welding process.
Detailed function of the TIG welding process.
The required current is supplied via the tungsten electrode at the core of the welding process in TIG welding. The tungsten electrode is the arc source that heats and liquefies the material to be welded.
The shielding gas streams from the gas nozzle to protect the heated material as well as the liquid weld pool from chemical reactions with the ambient air.
This process ensures high-quality weld seams.
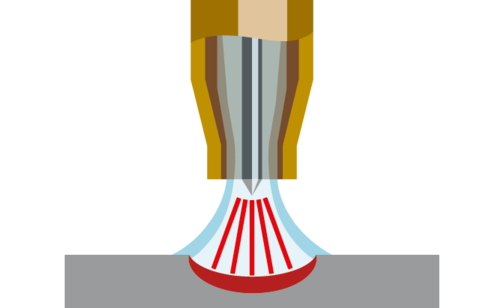
What is TIG welding?
TIG welding, or tungsten inert gas welding, is a fusion welding process with special properties that lead to precise, high-quality weld seams. TIG welding is used, among other places, in the aerospace industry.
The electric arc in TIG welding is generated between a tungsten electrode and the workpiece. The arc in TIG welding is highly intense and can be guided excellently.
Argon is usually used as a shielding gas to protect the arc and the welding zone, i.e. the liquid weld seam and the electrode in the torch, from oxygen without affecting the welding process itself.
Filler metals are generally not required for TIG welding. The weld is produced by welding a joint together.
If a filler metal is to be used anyway, it must be added to the liquid weld pool either manually or with a special cold wire feeder.
The welding technique of TIG welding is forehand welding. The filler metal is either fed in drop by drop or continually by holding the welding rod into the liquid weld pool throughout.
Since the filler metal is fed through the torch in MIG-MAG-welding, TIG torches differ slightly from MIG-MAG torches.
TIG welding is used where high quality and welds without spatter are needed and weld seam appearance is relevant. Among other things, these aesthetic requirements demand a high degree of precision in execution of welding tasks and turns TIG welding into a particularly challenging option.
TIG welding is suitable, among other things, for:
- Stainless steels
- Aluminium and nickel alloys
- Particularly thin sheets of aluminium and stainless steel
- Special materials like titanium
TIG welding material and gas combinations.
Aluminium and aluminium alloys.
- Procedure: TIG
- Wire electrode: depending on the material to be welded
- Shielding gas: Ar, He, or mixtures
General pipe and container construction.
- Procedure: TIG
- Wire electrode: WSG 1-3
- Shielding gas: Ar, He, or mixtures
Aviation and aerospace.
- Procedure: TIG
- Wire electrode: depending on the material to be welded
- Shielding gas: Ar, He, or mixtures
Advantages and disadvantages of TIG welding.
Advantages:
- Welding any metals
- Easy handling and good controllability
- Precise, high quality seams without spatter
- No rework
- Suitable for welding in all positions
- Good possibilities for mechanisation in orbital welding
- Excellent thin-sheet properties
Disadvantages:
- Low welding speeds
- High skill and experience necessary for execution
- Workpiece preparation is necessary
- Not suitable for higher workpiece thicknesses
Our solutions for TIG welding
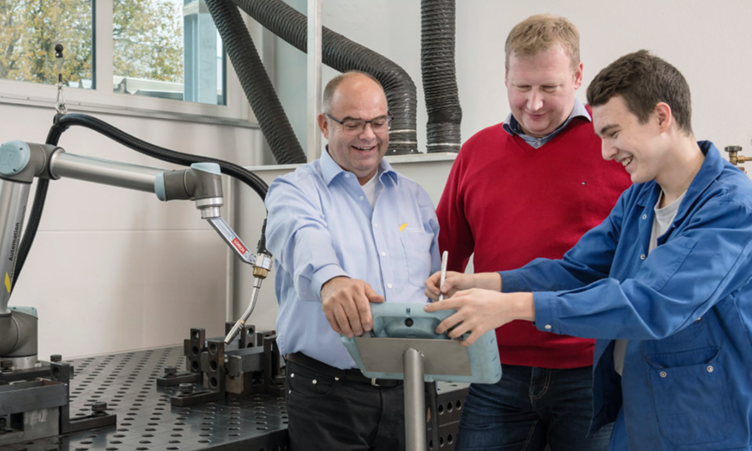
Always well-advised with close, personal, and honest support.
Are you interested in a Lorch welding unit with special aptitude for TIG welding but not quite certain of which model to choose yet? Do you have any other questions? The Lorch partner search will easily let you find a competent contact in your area to give you some personal advice.