Case: Hodapp GmbH & Co. KG Quick help against shortage of skilled workers.
Time-consuming small-series production characterises the daily routine at Hodapp.
Hodapp GmbH & Co. KG, specialising in the production of steel doors and gates, used to perform all welding manually. Welding now accounts for more than a third of total production. Small series of 80 or even 120 identical workpieces in particular are common in day-to-day business here. All workpieces must be welded individually in a time-consuming process. They must live up to the corresponding safety standards, a task made all the harder by the severe shortage of skilled workers in the region. Trained welding specialists are extremely rare as well.
Overview of Hodapp GmbH & Co. KG.
Simple programming.
The required welding parameters, such as sheet thickness, material, and throat thickness a, can be entered quickly via the Lorch Cobotronic software.
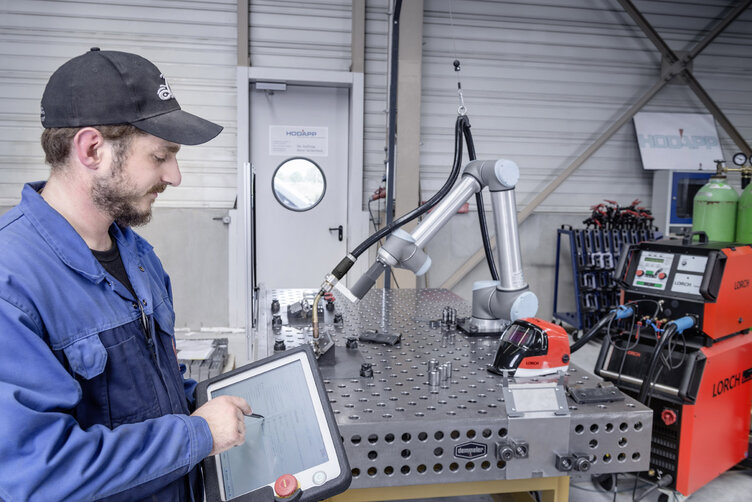
Colleague Cobot welds flexibly and perfectly reliably
The Lorch Cobot Welding Package allows Hodapp to guarantee consistently high weld seam quality, even at high volumes, and deploying more highly qualified welders where their specialist know-how is needed.
- Easy programming and operation
- Quick installation
- Relieves employees and compensates for shortage of skilled workers
High precision and enormous time savings.
The Cobot with S-RoboMIG XT double case system.
The Lorch welding Cobot is primarily used for applications that are difficult to weld by hand, for weld seams that require high precision and visual quality, and for labour- and time-intensive series production at Hodapp. The company has chosen the Cobot UR 10 with an arm reach of 1.30 metres for easy operation of two fixtures on the same welding table in order to further increase efficiency and reduce working time. Another important criterion for Hodapp’s decision was the option of combining the Lorch S-RoboMIG XT power source with a double case. This highlight optimally supports the internal processes since both steel and stainless steel are welded based on the order. The double case system provides both options after replacing only the welding torch on the Cobot. This enormously reduces equipment times.
Clear advantage: The Cobot arm length.
Benefit of the UR 10’s long arm: The next workpiece can already be inserted at a second fixture on the worktable while the Cobot is still welding at the first one.
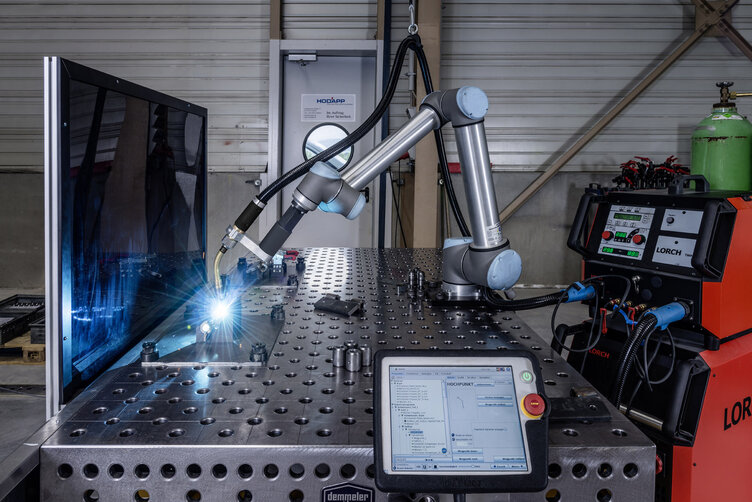
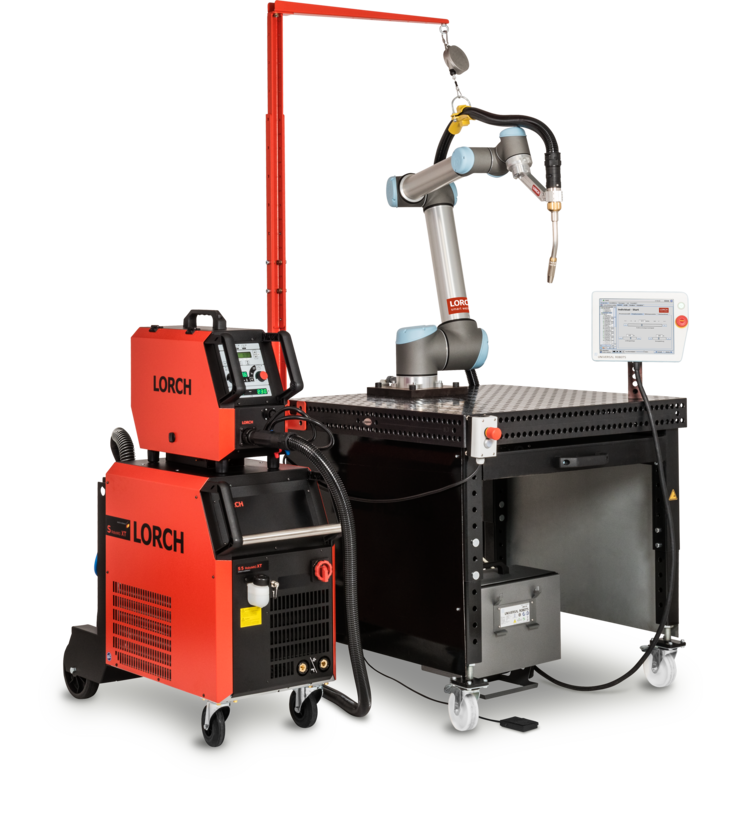
The Lorch Cobot Welding Package MIG-MAG: Get going now!
Cobot welding means collaborative robot welding for medium-sized companies. The MIG-MAG edition of the Lorch Cobot Welding Package is the ideal tool for economical welding automation in small and medium series production. What are you waiting for? The Lorch Welding Package MIG-MAG lets you start automating your welding production right away.
Downloads
Do you want to learn more about the Lorch Cobot Welding Package MIG-MAG? Technical data as well as further details on application and equipment can be found in the data sheet, and additional information is provided in the brochures: