Case: Karl Müller GmbH & Co. KG Lorch S-series: Perfect for demanding weld seams
Extraordinary demands on weld seams in trailer production.
Müller-Mitteltal follows the principle of “best quality for professional applications”. The medium-sized family-owned business from the area of Freudenstadt has conquered a leading position throughout Europe in the field of trailer manufacturing. Exceptionally high demands are placed on the quality of the weld seams in the production of customised trailers and low-loaders. High payloads require a precise and secure fit.
Overview of Karl Müller GmbH & Co. KG.
Fast and spatter-free welding with the S-series and SpeedPulse XT.
Weld seams require a high visual quality at Müller-Mitteltal. Nearly every single joint ends up visible after all. As a result, the individual sheets are precisely tacked beforehand. An ingenious design of longitudinal and transverse struts to keep the dead weight of the trailers at a minimum in spite their enormous transport loads produces many short weld seams subject to great stress.
The company now produces with 17 Lorch S-series MIG-MAG systems using the innovative SpeedPulse XT welding process. Not only does it speed up welding considerably but it has also minimised rework.
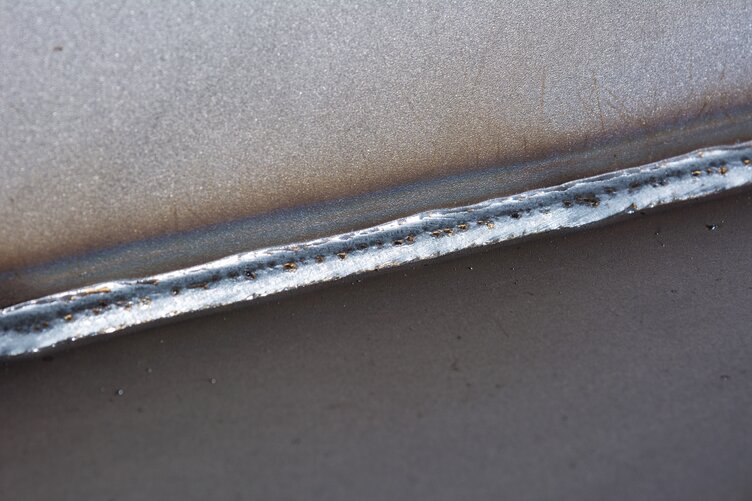
High-quality weld seam.
The joints also visually offer an optimised weld appearance. Difficult areas such as tack welds and uneven gaps can be easily removed thanks to SpeedPulse XT. Just weld over it.
Dynamic control is very helpful, as is the SpeedPulse XT welding process.
It allows welders to set a softer or harder arc depending on the work process or personal preferences.
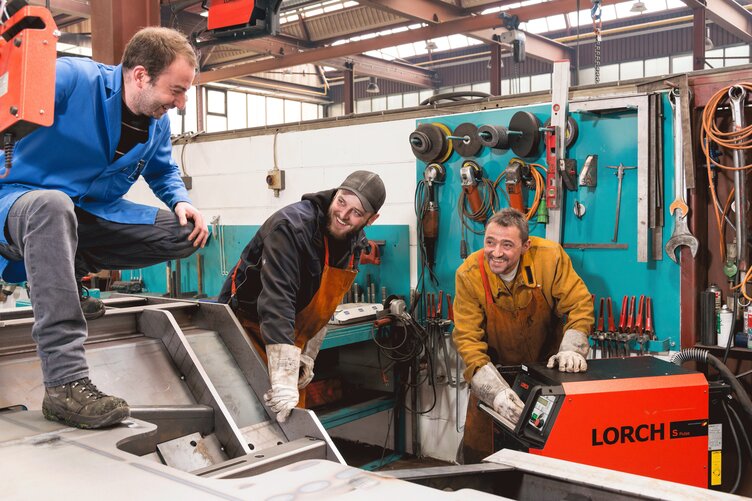
Easily master difficult welding situations.
Inherent proportional control enables optimal control of the welding process.
The SpeedPulse XT welding process optimises usage conditions at Müller-Mitteltal. Difficult welding situations, e.g. in corners, can be managed very well with the SpeedPulse XT welding process. The inherent proportional control patented by Lorch is a special advantage, allowing controller intervention without waiting for the pulse phase to end, and thereby permitting lightning-fast yet moderate control of the welding process.
This is particularly noticeable when welding over tack welds or unequal gap dimensions. While conventional arcs require great adjustments at times and tend to overshoot, the SpeedPulse XT arc length can be adjusted much more precisely.
Consequence: Over-welding can be done safely and without jerking. There are no more audible frequency changes and the tendency to splash decreases significantly. Start and end correction is also very helpful with the large number of short weld seams. In addition to arc length correction, this allows adjustment of the arc length specifically for the start and end phases and the problematic start and end craters to be completely avoided.
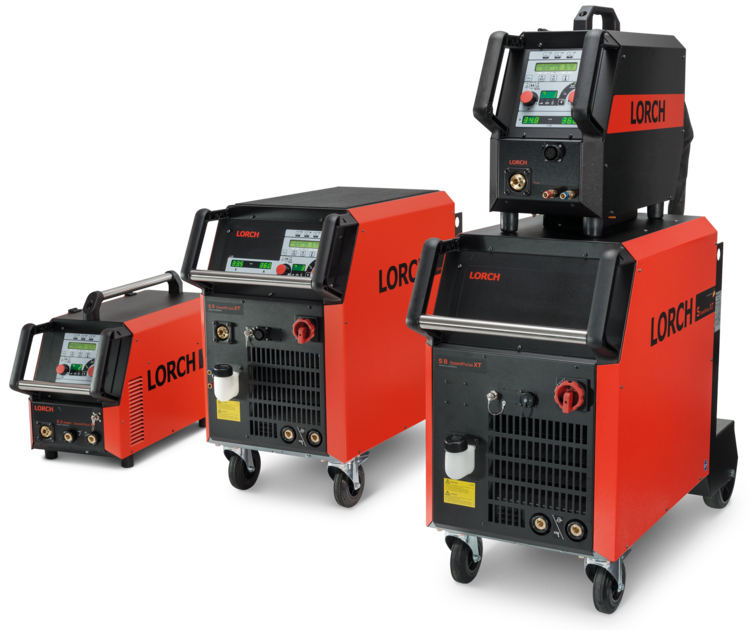
The S-series: Premium MIG-MAG welding units made to measure.
S-series welding units adapt perfectly to your needs, while MIG-MAG Speed processes combine greatest efficiency and quality. Configure the S series precisely to your needs to ensure that your system fits perfectly into the production environment and welding task.
On top of this, all S-series welding units are complemented by their intuitive operating concept that provides easy access to all setting options. Learn more now or find a competent Lorch partner near you for personal advice!
Downloads
Do you want to learn more about the Lorch S-series? Technical data as well as further details on application and equipment can be found in the data sheet, and additional information is provided in the brochures: