Case: Becchetti The new MicorMIG fleet reduces manufacturing costs while optimising production processes.
Italian medium-sized company benefits from speed processes and flexible upgrade options
Family-owned Becchetti company is looking back on eight decades of successful corporate history. Today, it has 40 employees and is a leading manufacturer of industrial vehicles in Italy. The company’s main focus is on production of semi-trailers with lengths of up to 13 metres and the assembly of construction cranes. Full renewal of the machinery had become necessary in the area of welding production. The new welding systems had to meet two important requirements in further significant production-cost reduction and production process quality increase at material thicknesses from 1 to 15 millimetres. The conversion to the innovative MicorMIG welding systems and Speed welding processes from Lorch has made MIG-MAG welding even faster with SpeedArc and SpeedUp. The option of adjusting the new fleet to growing weldingtechnical requirements at any time by applying upgrades allows the company to react quickly to individual customer requirements or changes on the market.
Overview of Costruzioni Meccaniche Becchetti Srl.
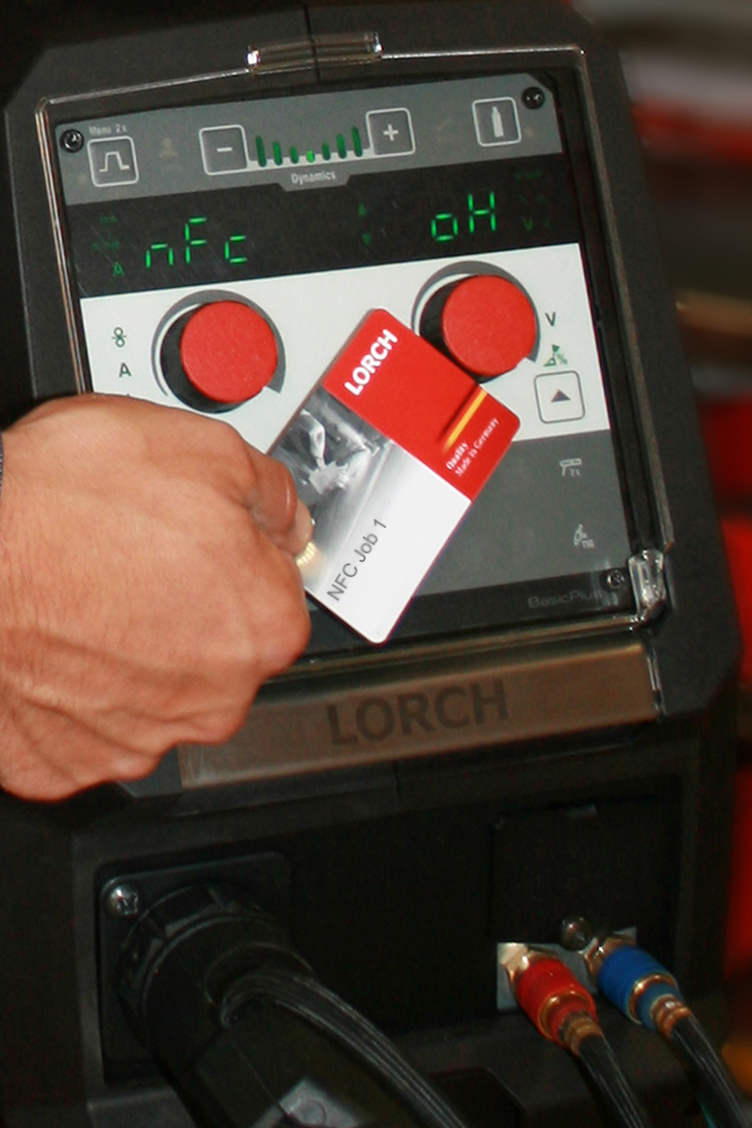
Highly useful in manufacture:
Synergic lines stored on NFC cards can be read in quickly and contact-free at any system.
Excellent weld seams and enormous time savings are achieved with SpeedArc and SpeedUp.
HIGH FLEXIBILITY THANKS TO UPGRADEABILITY OF THE MICORMIG SERIES.
The SpeedArc welding process has a high power density, achieving higher arc pressure on the weld pool. This makes MIG-MAG welding even faster while producing a particularly deep penetration into the base material. Many parts can now be welded in a single layer instead of multiple layers. The focused, stable arc reduces component distortion as well, while ensuring a better visual result of the weld seam. Additionally, the differentiated control technology of the Speed-Up process allows quick and virtually spatter-free weld seams even in the vertical direction. SpeedUp combines a high-current pulse phase (penetration) with a short arc phase (weld seam cooling), thereby ensuring reliable fusion penetration and the optimum throat thickness with a controlled energy input. The classic Xmas tree technique that requires plenty of skill and time is a thing of the past. Flexible adaptation of the new MicorMIG fleet to the respective welding requirements by way of upgrades is ideal for the company as well. Using the practical NFC technology, optimised welding values can be transferred to the systems at any time and productivity-increasing welding processes, welding programmes, and work-simplifying functions can be easily uploaded to any welding system as well.
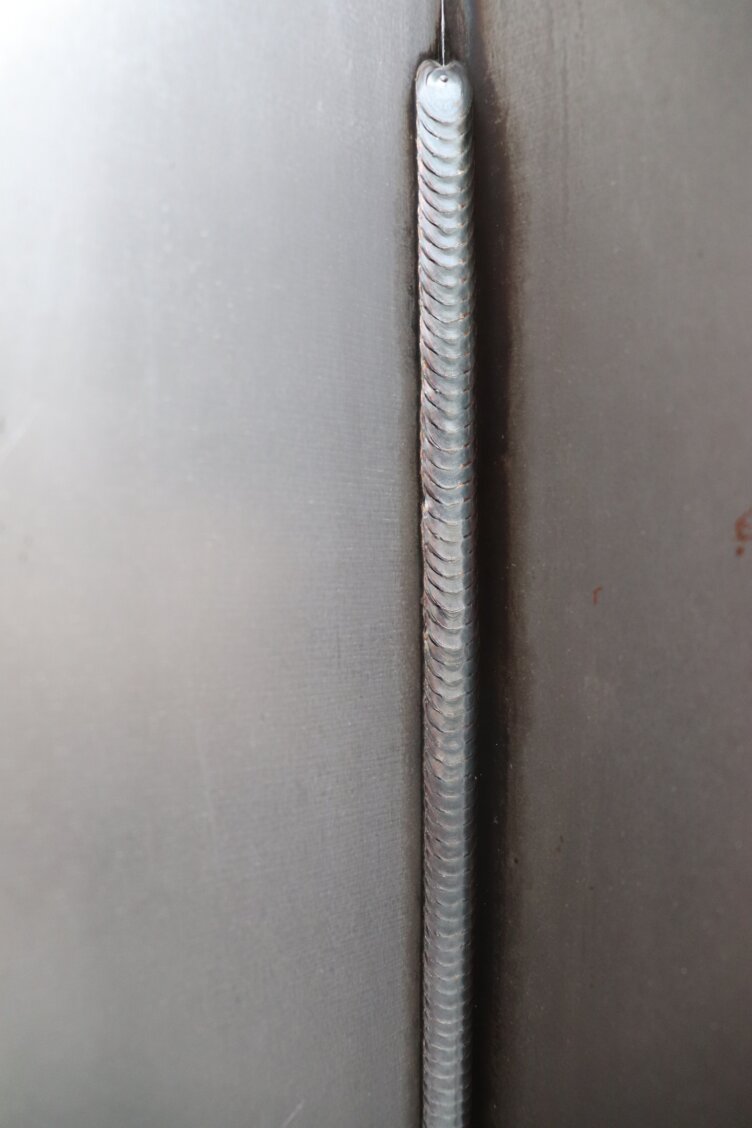
SpeedUp.
Vertical weld seams can be welded quickly and virtually spatter-free – without requiring any special skills and without any time-consuming triangular movement.
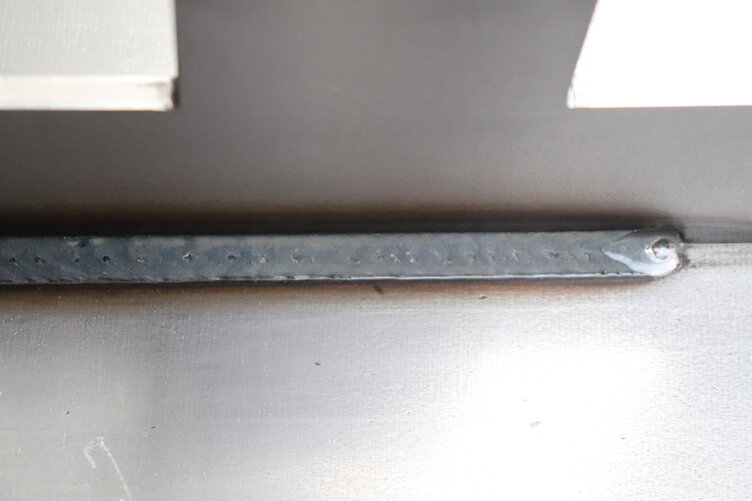
SpeedArc.
Parts that used to need welding in multiple layers can now be joined with a single weld seam.
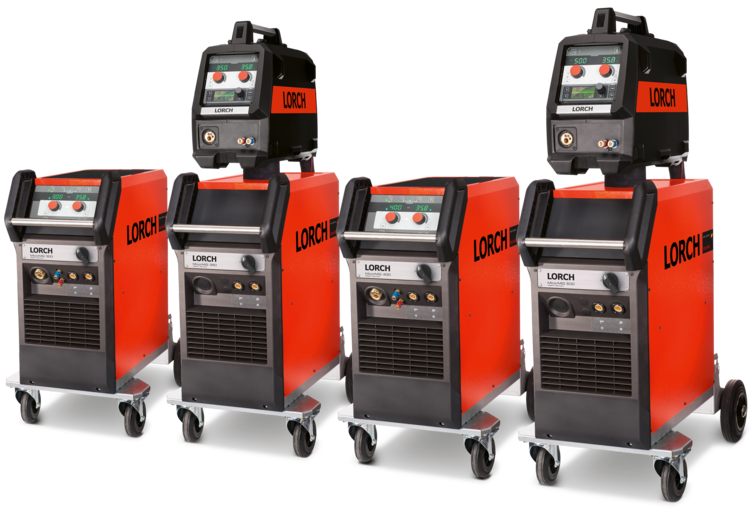
The MicorMIG series replaces the transformer with a future-proof inverter.
These modern and cost-efficient welding unit will keep you flexible: upgrade-capable and compatible with the innovative MIG-MAG Speed processes. the Lorch MicorMIG is setting standards and making switching to a modern, steplessly adjustable welding system simple and effective.
Downloads
Do you want to learn more about the Lorch Trac WL and MicorMIG series? Technical data as well as further details on application and equipment can be found in the data sheet, and additional information is provided in the brochures: